Manufacturing And Processing Of Filter Bags In India
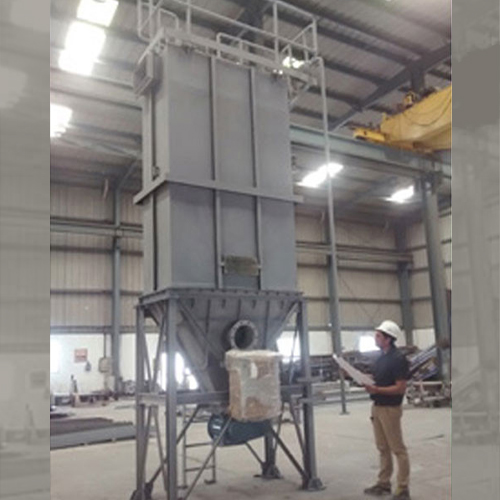
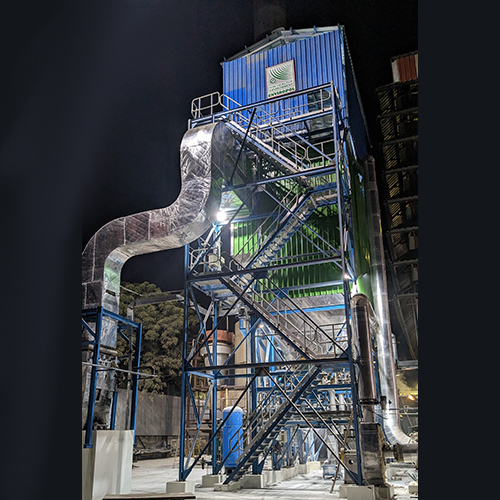
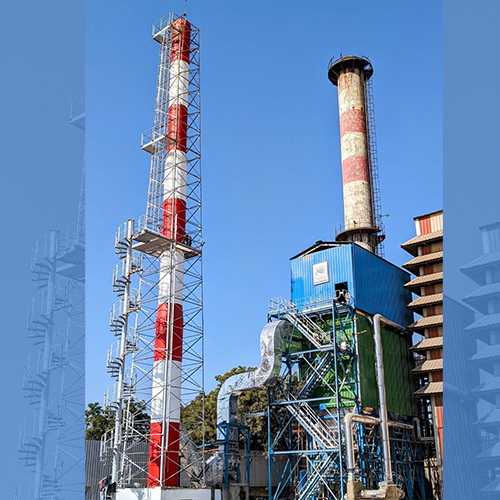
A bag filter, also known as a fabric filter or baghouse, is an air pollution control device designed to remove particulate matter (dust, particulates, and solid particles) from industrial gas streams. Bag filters are widely used in a variety of industries to improve air quality and ensure compliance with environmental regulations. They are particularly effective for capturing fine particles and have a straightforward and reliable design. Here's a description of the key components and operation of a bag filter:
Components of a Bag Filter:
- Housing: The bag filter is housed in a container or chamber that accommodates the filter bags and provides the necessary structural support.
- Filter Bags: The heart of the bag filter system, filter bags are cylindrical fabric tubes made of various materials (such as woven or felted fabric) that capture and retain particulate matter from the gas stream. These bags are suspended inside the housing.
- Inlet/Outlet Ducts: The industrial gas stream enters the bag filter through an inlet duct and exits through an outlet duct.
- Cleaning Mechanism: Bag filters often have a cleaning mechanism to remove accumulated dust from the surface of the filter bags. Common cleaning methods include reverse air, pulse-jet, or mechanical shaking.
Operation of a Bag Filter:
- High Efficiency: Bag filters are highly efficient at capturing fine particulate matter, making them effective in improving air quality.
- Versatility: They can be used in various industrial applications to control dust emissions and particulate matter.
- Economical: Bag filters offer cost-effective solutions for air pollution control, given their efficient operation and relatively low maintenance requirements.
- Low Pressure Drop: They typically have a low pressure drop, which minimizes energy consumption in the gas-handling system.
- Scalability: Bag filters can be easily scaled up or down to meet specific industrial needs.
Bag filters are commonly used in industries such as cement manufacturing, power generation, food processing, pharmaceuticals, metals production, woodworking, and many more where the control of particulate emissions is critical for environmental compliance and workplace safety.
Industrial application for bag filter
Bag filters are widely used in various industrial applications where the control of particulate emissions is crucial for maintaining air quality, ensuring regulatory compliance, and protecting equipment and processes. Some common industrial applications for bag filters include:
- Cement and Concrete Industry:
- Bag filters are used to capture fine particulates generated during the production of cement, concrete, and various cement-related processes, such as kiln emissions, clinker cooling, and coal mills.
- Power Generation:
- In coal-fired power plants, bag filters help control particulate emissions from flue gases. They are also used in biomass and waste-to-energy power plants.
- Metals and Foundry Industry:
- Bag filters capture dust and fumes generated in metal smelting, casting, and metalworking processes, reducing emissions of particulate matter, heavy metals, and volatile organic compounds (VOCs).
- Food and Beverage Processing:
- Bag filters are employed to control dust and particulate emissions in various food processing operations, including grain milling, grain handling, and packaging.
- Pharmaceutical Manufacturing:
- In pharmaceutical production, bag filters help control emissions of fine powders, active pharmaceutical ingredients (APIs), and other particulates during the manufacturing process.
- Chemical Manufacturing:
- Bag filters are used to capture dust and particulates in various chemical production processes, including drying, blending, and mixing operations.
- Mineral and Mining Industry:
- Bag filters help control dust emissions from mining, crushing, screening, and material handling operations.
- Woodworking and Furniture Manufacturing:
- Bag filters capture wood dust and particulates produced during cutting, sanding, and finishing operations in the woodworking industry.
- Textile Industry:
- Bag filters are used in textile manufacturing to control dust and lint emissions from operations such as carding, spinning, and weaving.
- Asphalt and Aggregate Production:
- In the production of asphalt and aggregate materials, bag filters are used to capture dust and particulates generated during crushing, screening, and mixing processes.
- Phosphate and Fertilizer Production:
- Bag filters help control dust emissions from phosphate and fertilizer production facilities, ensuring compliance with environmental regulations.
- Chemical Processing:
- Bag filters are applied to control emissions of fine powders, catalysts, and particulates in chemical processing and refining operations.
- Plastics and Rubber Manufacturing:
- Bag filters capture dust and particulates produced in the manufacturing of plastic and rubber products.
- Waste Incineration:
- In waste incineration plants, bag filters are used to control emissions of particulates, heavy metals, and acid gases generated during the combustion of waste materials.
- Paper and Pulp Industry:
- Bag filters help control particulate emissions from paper and pulp production processes, including recovery boilers and dust collection systems.
- Ferrous and Non-Ferrous Metal Production:
- Bag filters are used to capture particulates, fumes, and dust produced in the production of both ferrous and non-ferrous metals.
- Paint and Coatings Manufacturing:
- Bag filters help control emissions of powders and particulates in the manufacturing of paints, coatings, and pigments.
- Municipal Water and Wastewater Treatment:
- In sewage treatment plants, bag filters are used for odor control by capturing and removing odorous particles and contaminants.
Bag filters are chosen for these applications based on their ability to efficiently capture particulates, their cost-effectiveness, and their adaptability to various industrial processes and gas volumes. They play a crucial role in reducing air pollution and maintaining air quality in industrial settings.